Condition-Based Maintenance System Using AVEVA PI and AVEVA Asset Framework

Challenge
Inefficiencies in Traditional Maintenance: Industries have long relied on time-based maintenance and manual monitoring, facing significantchallenges:
Reactive Approach: Maintenance is often performed on a fixed schedule, resulting in either premature servicing or, worse, unexpected failures.
Operational Downtime: Scheduled maintenance can lead to unnecessary downtime, impacting productivity.
Resource Intensity: Manual data collection and analysis are labor-intensive and prone to error.
Lack of Predictive Insights: Traditional methods lack the ability to predict failures accurately, leading to reactive rather than proactive maintenance strategies.
Disparate Data Systems: Multiple, unintegrated data sources limit visibility and inhibit effective decision-making.
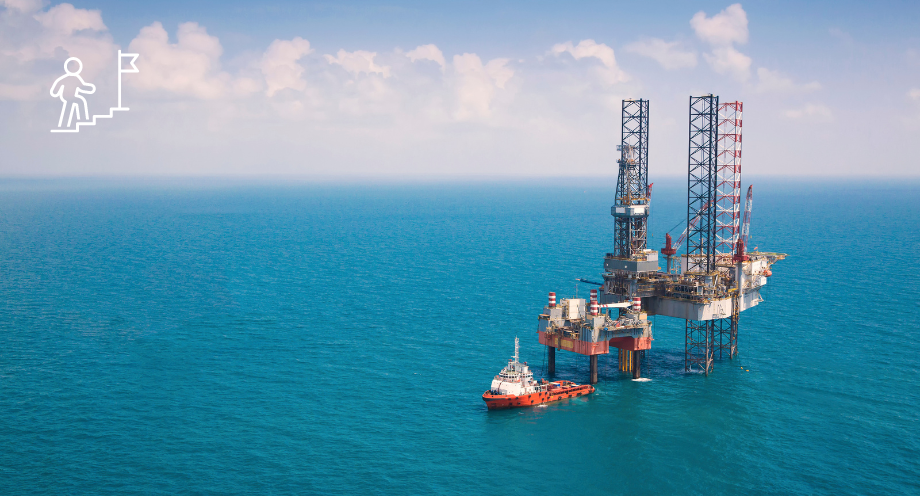
Solution
Transition to Condition-Based Maintenance (CBM): The implementation of a CBM system using AVEVA PI and AVEVA Asset Framework offers a transformative approach:
Real-Time Monitoring: Sensors installed on equipment continuously feed data into the AVEVA PI System, providing a single source of truth for real-time and historical data analysis.
Advanced Analytics: The system employs streaming analytics and machine learning (ML) models to interpret data, generating predictive maintenance insights that surpass traditional methods.
Dynamic Asset Health Assessment: Unlike periodic assessments, the system enables dynamic, real-time evaluation of asset health, identifying critical equipment changes early on.
Seamless Data Integration: PI Interfaces and Connectors link various data sources, from SCADA systems to CMMS, ensuring efficient and secure data flow across the enterprise.
Automated Alerts and Notifications: Custom alerts based on predefined parameters allow maintenance teams to act swiftly, mitigating potential issues before they escalate.
Scalability and Flexibility: The PI System supports a wide range of equipment, from gas and steam turbines to pumps and compressors, making it applicable to any sensor-equipped asset.
Key Features
"Transform your maintenance strategy from reactive to predictive with AVEVA's Condition-Based Maintenance system, reducing costs by up to 20% and maximizing equipment lifespan through real-time data and advanced analytics."
Outcome
Enhanced Operational Efficiency and Cost Savings:
Reduced Maintenance Costs: Industry examples have demonstrated that the transitioning from reactive to predictive maintenance can decrease overall maintenance expenses by up to 20% within five years.
Increased Equipment Lifespan: By basing maintenance decisions on data rather than intuition, equipment longevity is maximized, and unnecessary replacements are avoided.
Improved Asset Availability: The system prioritizes maintenance based on asset health and criticality, optimizing production capacity and reducing downtime.
Higher Reliability and Safety: Real-time insights enable proactive issue resolution, enhancing safety and reducing the likelihood of catastrophic failures.
Comprehensive Data Utilization: By leveraging real-time and historical data, the system facilitates root cause analysis, environmental monitoring, and regulatory compliance, supporting broader asset management strategies.
Digital Transformation Enablement: CBM serves as a foundational step toward a larger digital transformation journey, integrating with ERP and other systems for a holistic approach to asset management.