From manual to automated production reporting
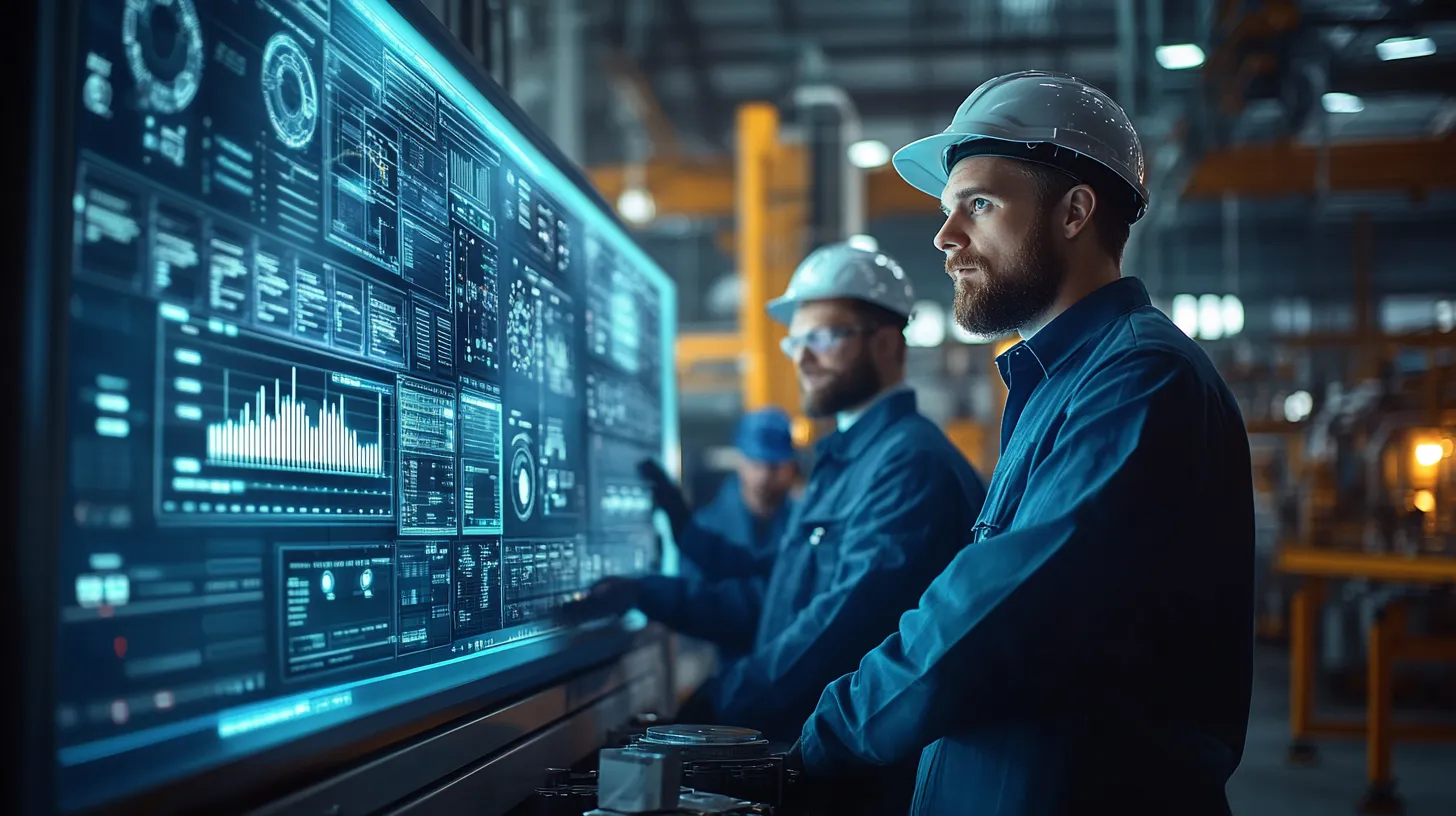
Challenge
Reliable production reports are of outmost importance in most manufacturing industries as trusted and approved data shared with internal departments and external stakeholders, ensuring that everyone is aligned on current production levels and operational performance. Production reports are today still being manually maintained in Excel sheets, or similar, which requires excessive manual labor to populate with data, to maintain, and package in a distributable format. In other cases, reports are based on custom built proprietary software in which simple editing of report content such as data sources, changing values and visuals are difficult, if possible at all, without making changes to the software itself.
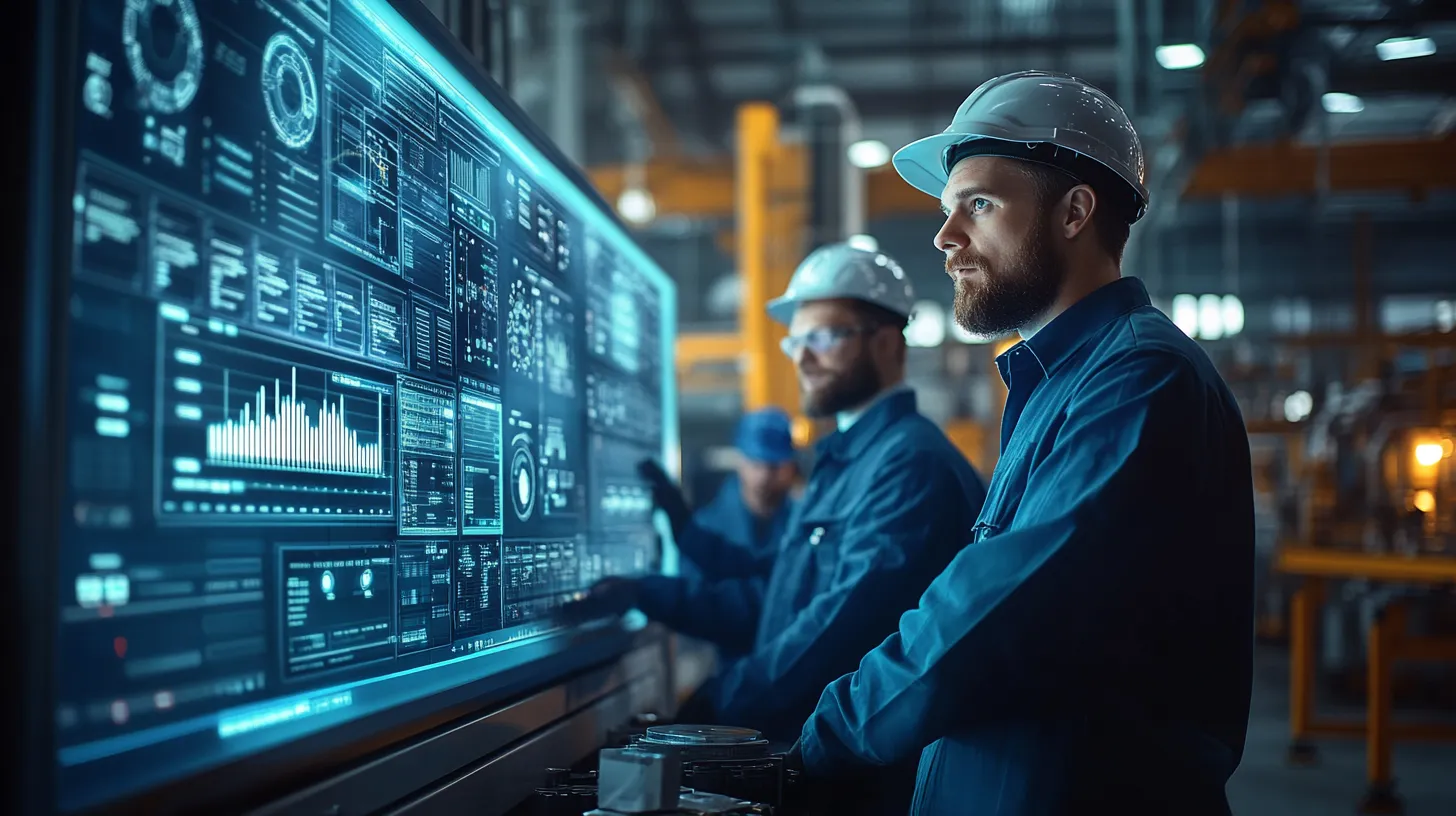
Solution
By transitioning to automated reporting solutions based on off-the-shelf software from AVEVA and Dimension Software, companies can transform their production reporting processes, overcoming the inefficiencies and constraints of manual data entry and rigid proprietary systems.
Lower operating costs and reduce manual labour: This shift significantly reduces operating costs by minimising manual labour and streamlining the interface between human and machine, allowing automation to handle the heavy lifting. As a result, the reporting process becomes more efficient, with reports automatically populated, formatted, and ready for verification and distribution, freeing up valuable employee time and resources.
Trust your data: Automated solutions enhance data accuracy and consistency by standardising inputs and automating calculations, thereby reducing the risk of human error. This reliability ensures that reports are consistently accurate and trustworthy, which is essential for trend analysis and informed decision-making.
Scale with flexibility: The system’s scalability and flexibility also mean that as the company’s data needs grow, the reporting infrastructure can easily adapt without requiring costly software modifications. This makes it possible to implement changes quickly and efficiently, enabling the business to scale its reporting capabilities in line with its evolving needs.
Key Features
Free up employee time by transitioning to automated reporting.
Outcome
Reports that can be trusted is key. Standardise data inputs and automate calculations to reduce errors and ensuring consistent, accurate reports. This reliability enhances trend analysis and informed decision-making.
Make the transition from manual and proprietary solutions to easy-to-use automated solutions. Off-the-shelf software offers superior flexibility and reliability.
By using Asset Intellect from Dimension Software, it is possible to not only reduce the cost of procurement, but drastically reduces the time, effort and cost of operating production reporting.
At the same time, it can significantly reduce the risk of human error and ensure that the correct numbers are used in the report.